Entwicklung simulationsgestützter Assistenten für die Extrusion (ExtrA)
/in Allgemein /von SHS_adminIn diesem Projekt zur Entwicklung simulationsgestützter Assistenten für die Extrusion wird Expertenwissen über den Kunststoffverarbeitungsprozess mit Ergebnissen aus Live-Computersimulationen in einem cyberphysischen System kombiniert, um automatisiert Informationen zur Optimierung des Produktionsprozesses zu generieren. Dazu werden die unterschiedlichen, für die Prozessoptimierung relevanten Expertisen und praktischen Erfahrungen mit inter- und transdisziplinären Forschungsmethoden im Fachbereich Technik und Diversity erschlossen und zur Verbesserung der Produktivität, Produktqualität, Bedienbarkeit und Diversität implementiert.
Bei der Herstellung von Kunststoff-Halbzeugen wie beispielsweise Kunststoffrohren, -hohlstäben, -vollstäben etc. wird Kunststoffgranulat in einem Extruder (1) aufgeschmolzen. Die entstehende Kunststoffschmelze strömt aufgrund des im Extruder erzeugten Druckes durch ein Extrusionswerkzeug (2), welches somit die zähflüssige Schmelze in die Produktform umlenkt. Nach dem Verlassen des Extrusionswerkzeuges wird die Produktgeometrie in einer Kühlstrecke (3) kalibriert und gezielt abgekühlt, so dass ein qualitativ hochwertiges Produkt entsteht. Die Parametrierung des gesamten Prozesses (Extruder, Werkzeug, Kühlstrecke) übernimmt ein Maschinenbediener mit seinem spezifischen Know-how (4). Ziel des Projektes ist es, auf der Basis von Live-Computersimulationsmöglichkeiten sowie einer angekoppelten Expertendatenbank einen möglichst autarken Betrieb einer Extrusionslinie zu ermöglichen. Dazu werden sämtliche Messdaten, die bereits an der Extrusionslinie vorliegen (z.B. in der Extrudersteuerung) ausgelesen und weitere Prozessparameter über zusätzliche Sensoren erfasst. Diese Daten werden in einer zentralen Datenbank gespeichert. Drei verschiedene Simulationssysteme für die Subsysteme 1, 2 und 3 lesen die Live-Prozessdaten aus der Datenbank und erzeugen Simulationsergebnisse. Diese Simulationsergebnisse dienen als zusätzliche Informationen über den Prozess und beinhalten nicht messbare Größen sowie prognostische Werte. Sämtliche vorhandene Informationen werden einem Softwaresystem übergeben, welches zusätzlich über implementiertes Expertenwissen verfügt und auf der Basis verschiedener Methoden (Fuzzy-Logik, künstliche neuronale Netze, Machine Learning, Deep Learning) dem Maschinenbediener Verbesserungsmöglichkeiten vorschlägt oder die Linie autark betreibt.
Mit dem Forschungsvorhaben wird ein wertvoller Beitrag auf dem Weg zur intelligenten und flexiblen Produktion geleistet. Denn intelligente Systeme sammeln vielfältige Daten und erlauben somit eine sukzessive Erneuerung der Produkte und die standortunabhängige Optimierung der Prozesse. Gleichzeitig kann das Produkt günstiger und kundennäher ausgelegt werden. Die Technologien werden damit individualisiert.
Mit dem Forschungsvorhaben soll erstmalig eine innovative Gesamtlösung des extrudierenden Maschinensystems entwickelt werden. Damit ist das System in der Lage live und ohne Bedienereingriff Automatisierungsstrategien zu generieren. Eine derart konsequente Automatisierung und gegenseitige Verzahnung von computergestützten Systemen basierend auf realen Prozessdaten in einer Live-Umgebung hätte folglich einen weltweiten Alleinstellungswert und wurde bis dato in anderen Forschungsaktivitäten in der Form nicht realisiert.
Dieses Projekt wird durch die Europäische Union und das Land Nordrhein-Westfalen gefördert.
Kontakt
Sekretariat:
Dr. Anne Walter
Öffnungszeiten:
Mo.-Fr.: 08.00 – 17.00
Tel.: +49 2064 970 9370
E-Mail: office@shs-plus.de
SHS plus GmbH in Dinslaken
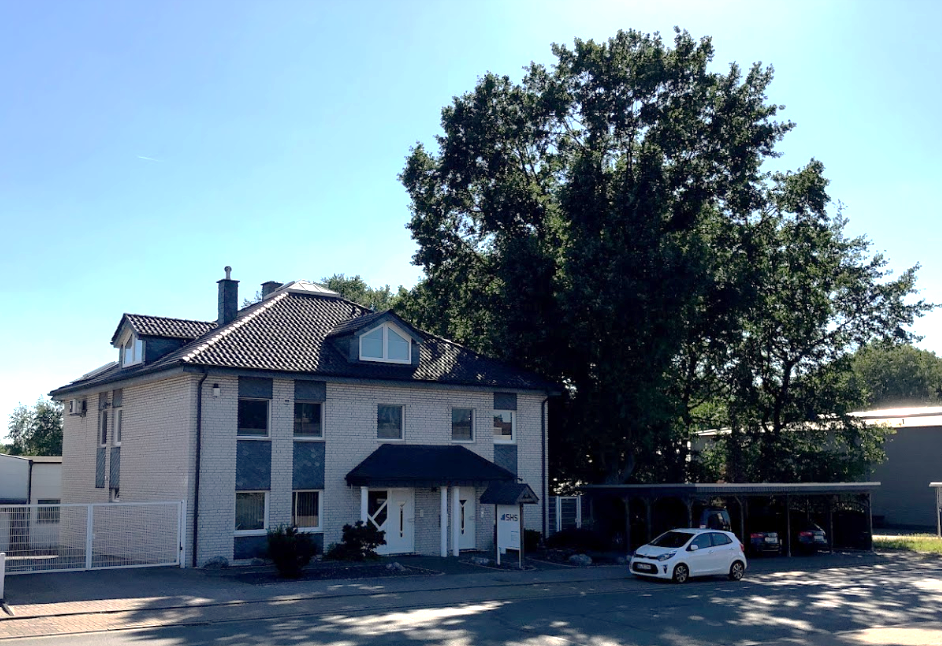
Seiten
- Ansprechpartner
- Automation
- Autorisierungen
- Consulting
- Datenschutzerklärung
- Extrusion-Training
- FAQ
- Funktionen – Skills
- Impressum
- Individuelle Steuerungen
- Partnerprogramm
- Philosophie
- pressureGUARD
- Referenzen
- Schnecken- und Werkzeugsimulation
- Seminare
- SHS plus GmbH
- Simulation
- Startseite
- Systembeschreibung
- temperatureGUARD
- Virtuelle Assistenzsysteme
Extrusion Training
- Automatisierte Situationsanalyse mit virtueller Assistenz – Vipra
- Ist virtuelle Assistenz so etwas wie ein MDE/BDE System?
- Wie können moderne Simulationsmethoden die Kühlstreckenauslegung in der Profilextrusion verbessern?
- Wofür benötige ich eigentlich eine Stützluftregelung in der Extrusion?
- Wann rechnet sich eine Durchsatzüberwachung?
- OPC UA – Was ist das eigentlich?
- Checkliste – Was tun in Zeiten mit geringer Produktionsauslastung?
- SHS Corona Hilfe
- Kann ich die Kühlleistung erhöhen, wenn ich die Kühltanks aneinanderschraube?
- Extruderdimensionierung & Schneckendurchmesser – was Sie beachten sollten…